In the diverse world of textiles, nonwoven fabrics stand out as versatile and innovative materials with a production process that sets them apart from traditional woven or knitted fabrics. From disposable medical gowns to durable geotextiles, the nonwoven fabric production process weaves a tapestry of applications. Let’s dive into the fascinating journey of how these unique fabrics come to life.
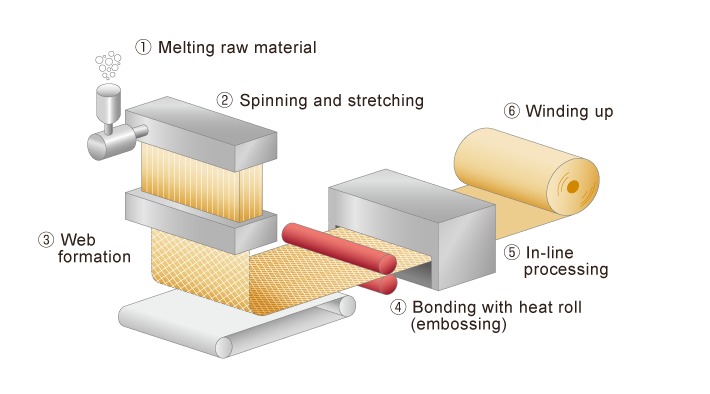
1. Raw Material Selection:
The journey begins with the selection of raw materials. Nonwoven fabrics can be crafted from a variety of fibers, including synthetic polymers (such as polypropylene, polyester, or nylon) or natural fibers (such as cotton or viscose). The choice of material depends on the intended use and desired properties of the final nonwoven product.
2. Web Formation in Nonwoven Fabric Production:
The heart of nonwoven fabric production lies in web formation. Unlike traditional fabrics that are created through weaving or knitting, nonwoven fabrics are made by entangling or bonding fibers together. There are several methods for forming the initial web:
Dry-Laid Process: Fibers are carded and laid down in a random or specific orientation. This can be done through air-laying or carding machines.
Wet-Laid Process: Fibers are suspended in water and formed into a web. This process is common for cellulose-based fibers like wood pulp.
Spunbond Process: Extruded continuous filaments are laid onto a moving belt, creating a web. This process is particularly common for synthetic fibers.
Meltblown Process: Molten polymer is extruded through fine nozzles, creating microfibers that are blown onto a collector. This process is crucial for creating fine and lightweight nonwoven fabrics.
3. Bonding in Nonwoven Fabric Production:
Once the web is formed, the next step is bonding the fibers to give the fabric integrity and strength. There are various bonding methods:
Thermal Bonding: Heat is applied to the web, melting the fibers at contact points and creating bonds.
Chemical Bonding: Adhesive chemicals are applied to the web, bonding the fibers together.
Mechanical Bonding: Needles or rollers physically interlace the fibers, creating a cohesive fabric.
Hydroentanglement: High-pressure water jets entangle the fibers, providing strength to the fabric.
4. Finishing and Treatment in Nonwoven Fabric Production:
Post-bonding, the nonwoven fabric may undergo additional treatments based on its intended application. This could include treatments for water repellency, flame resistance, antimicrobial properties, or dyeing processes.
5. Cutting and Winding:
The finished nonwoven fabric is then cut and wound into rolls or sheets, ready for distribution or further processing by manufacturers of end-products.
6. Diverse Applications:
Nonwoven fabrics find applications across a spectrum of industries:
Medical and Hygiene: Disposable surgical gowns, diapers, and sanitary products.
Geotextiles: Erosion control, soil stabilization, and drainage systems.
Automotive: Car interiors, filtration systems, and noise insulation.
Apparel: Interlinings, shoe components, and disposable clothing.
Home and Furnishings: Upholstery, bedding components, and cleaning wipes.
7. Sustainability Considerations:
As the textile industry gravitates toward sustainability, advancements in nonwoven fabric production include the use of recycled fibers and bio-based materials. These initiatives aim to reduce the environmental impact of nonwoven fabrics and align with the principles of a circular economy.
Conclusion: A Fabric of Endless Possibilities
The nonwoven fabric production process is a symphony of techniques, blending raw materials, web formation, bonding, and finishing to create fabrics with diverse characteristics. From medical essentials to automotive components, nonwoven fabrics have woven themselves into the fabric of our daily lives, offering a world of possibilities that extend far beyond traditional textiles. As technology advances and sustainability takes center stage, the journey of nonwoven fabrics continues to evolve, promising a future where innovation and responsibility coalesce in the world of textiles.
About POLYESTER FIBERS
POLYESTER FIBERS We partner with numerous factories and manufacturers in Viet Nam and other Asian countries.We supply various and different polyester staple fiber such as hollow conjugate siliconized and non-siliconized, hollow non conjugated fiber, hollow slick fiber, black solid fiber, brown fiber, green fiber, filling fiber, polyester fiber, recycled polyester fiber, spinning fiber. All are GRS and OEKO TEX certified.
Our polyester staple fiber is used as raw material for the production of several industrial applications such as polyester pillow filling, stuffed toys, cushion, comforters, sofa, mattress, bedding sheet, quiltings, wadding, padding, non-wovens, geotextile, automotive, abrasive products for domestic and industrial use, yarn for textile flooring (carpets and moquette), shoes, special filters and much more.
Our recycled Polyester Staple Fiber is of good quality and competitive price, which is used in the application of filling polyester pillows, mattress, cushions, quilting, comforters, padding, wadding, stuffed toys, carpets, felts, automotive nonwoven industry and home textiles.
We are well-known for our excellent customer service and we would like to have long-term business cooperation with customers from all over the world.
Please contact us for long-term cooperation!
Mr. HARRY
Website: vietnamrecycledfiber.com
Youtube: Vietnam Recycled Polyester Fiber